Plastic extrusion for tubing, profiles, and custom shapes
Plastic extrusion for tubing, profiles, and custom shapes
Blog Article
A Comprehensive Guide to the Refine and Benefits of Plastic Extrusion
In the substantial world of production, plastic extrusion emerges as a important and very effective procedure. Translating raw plastic into continual profiles, it deals with a wide variety of sectors with its exceptional adaptability. This overview intends to clarify the detailed steps entailed in this method, the kinds of plastic appropriate for extrusion, and the game-changing advantages it brings to the market. The following discussion guarantees to unravel the real-world effects of this transformative process.
Recognizing the Fundamentals of Plastic Extrusion
While it may appear complex at initial look, the process of plastic extrusion is basically straightforward. The procedure starts with the feeding of plastic product, in the kind of granules, pellets, or powders, into a heated barrel. The shaped plastic is then cooled, strengthened, and reduced right into preferred lengths, finishing the procedure.
The Technical Refine of Plastic Extrusion Explained

Kinds of Plastic Suitable for Extrusion
The option of the best kind of plastic is an essential facet of the extrusion process. Different plastics offer one-of-a-kind residential or commercial properties, making them much more suited to particular applications. Comprehending these plastic kinds can substantially enhance the extrusion procedure.
Comparing Plastic Extrusion to Various Other Plastic Forming Methods
Recognizing the kinds of plastic ideal for extrusion paves the means for a more comprehensive discussion on how plastic extrusion piles up against other plastic developing techniques. Plastic extrusion is unequaled when it comes to creating continuous profiles, such as gaskets, pipes, and seals. It also allows for a consistent cross-section along the length of the item.
Key Advantages of Plastic Extrusion in Manufacturing
In the realm of manufacturing, plastic extrusion uses lots of substantial advantages. One notable advantage is the cost-effectiveness of the process, that makes it an economically attractive production method. Additionally, this method offers premium item adaptability and enhanced manufacturing rate, therefore increasing overall manufacturing effectiveness.
Cost-efficient Production Technique
Plastic extrusion leaps to the center as a cost-effective manufacturing technique in production. This process stands out for its capacity to create high volumes of product rapidly and effectively, providing makers with significant savings. The primary cost benefit is the ability to utilize much less costly basic materials. Extrusion utilizes thermoplastic products, which are less expensive contrasted to metals or porcelains. Additionally, the extrusion process itself is reasonably simple, lowering labor costs. Additionally, plastic extrusion needs much less power than standard manufacturing techniques, adding to lower operational expenses. The procedure also reduces waste, as any kind of malfunctioning or excess materials can be recycled and recycled, giving another layer of cost-effectiveness. Generally, the economic advantages make plastic extrusion a highly appealing choice in the production market.
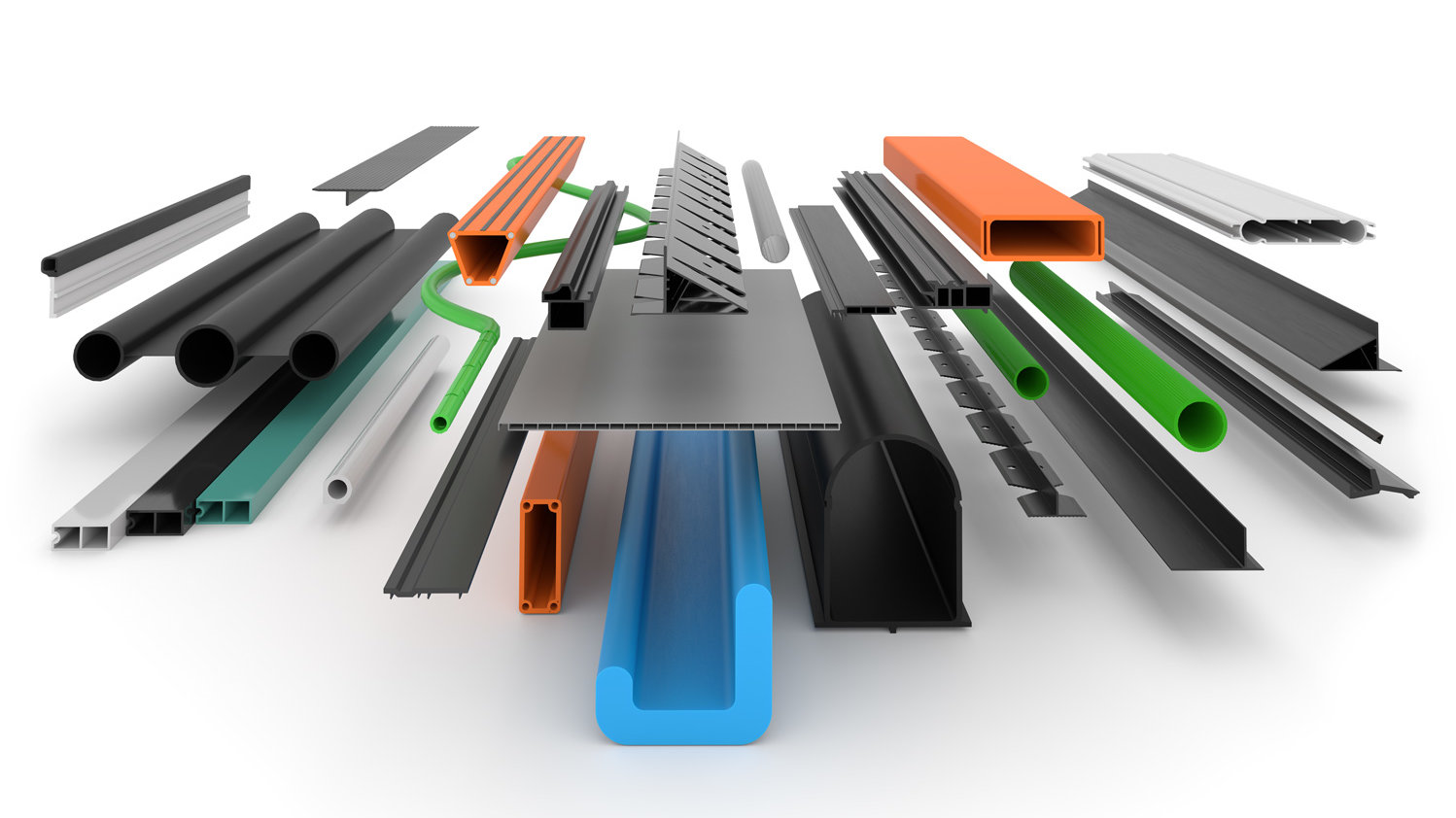
Superior Product Flexibility
Past the cost-effectiveness of plastic extrusion, another substantial benefit in producing depend on its remarkable product flexibility. This process permits the production of a vast variety of products with differing sizes, forms, and styles, from simple plastic sheets to complex accounts. The flexibility is attributed to the extrusion die, which can be personalized to generate the this desired product layout. This makes plastic extrusion an ideal service for industries that call for tailored plastic components, such as auto, construction, and product packaging. The capability to generate diverse products is not only advantageous in conference particular market needs however also in making it possible for producers to discover new item lines with very little capital expense. In essence, plastic extrusion's item flexibility cultivates advancement while enhancing functional efficiency.
Improved Manufacturing Rate
A considerable advantage of plastic extrusion exists in its enhanced production rate. Few other production procedures can match the speed of plastic extrusion. Additionally, the capacity to keep constant high-speed manufacturing without sacrificing product quality sets plastic extrusion apart from other methods.
Real-world Applications and Influences of Plastic Extrusion
In the world of manufacturing, the strategy of plastic extrusion holds extensive value. The economic benefit of plastic extrusion, primarily its high-volume and economical outcome, has actually transformed manufacturing. The market is persistently aiming for technologies in naturally degradable and recyclable materials, suggesting a future where the advantages of plastic extrusion can be retained without endangering ecological sustainability.
Final thought
Finally, plastic extrusion is a extremely effective and efficient technique of transforming basic materials right into varied products. additional hints It provides numerous advantages over other plastic creating approaches, consisting of cost-effectiveness, high outcome, marginal waste, and style versatility. Its impact is exceptionally felt in various markets such as building and construction, auto, and durable goods, making it a crucial procedure in today's manufacturing landscape.
Delving much deeper right into the technical procedure of plastic extrusion, it starts with the choice of the proper plastic material. Once cooled down, the plastic is reduced into the required sizes or wound onto reels if the item is a plastic movie or sheet - plastic extrusion. Comparing Plastic Extrusion to Various Other look at this site Plastic Forming Techniques
Comprehending the kinds of plastic appropriate for extrusion leads the method for a broader discussion on just how plastic extrusion stacks up versus other plastic forming approaches. Few various other manufacturing procedures can match the speed of plastic extrusion.
Report this page